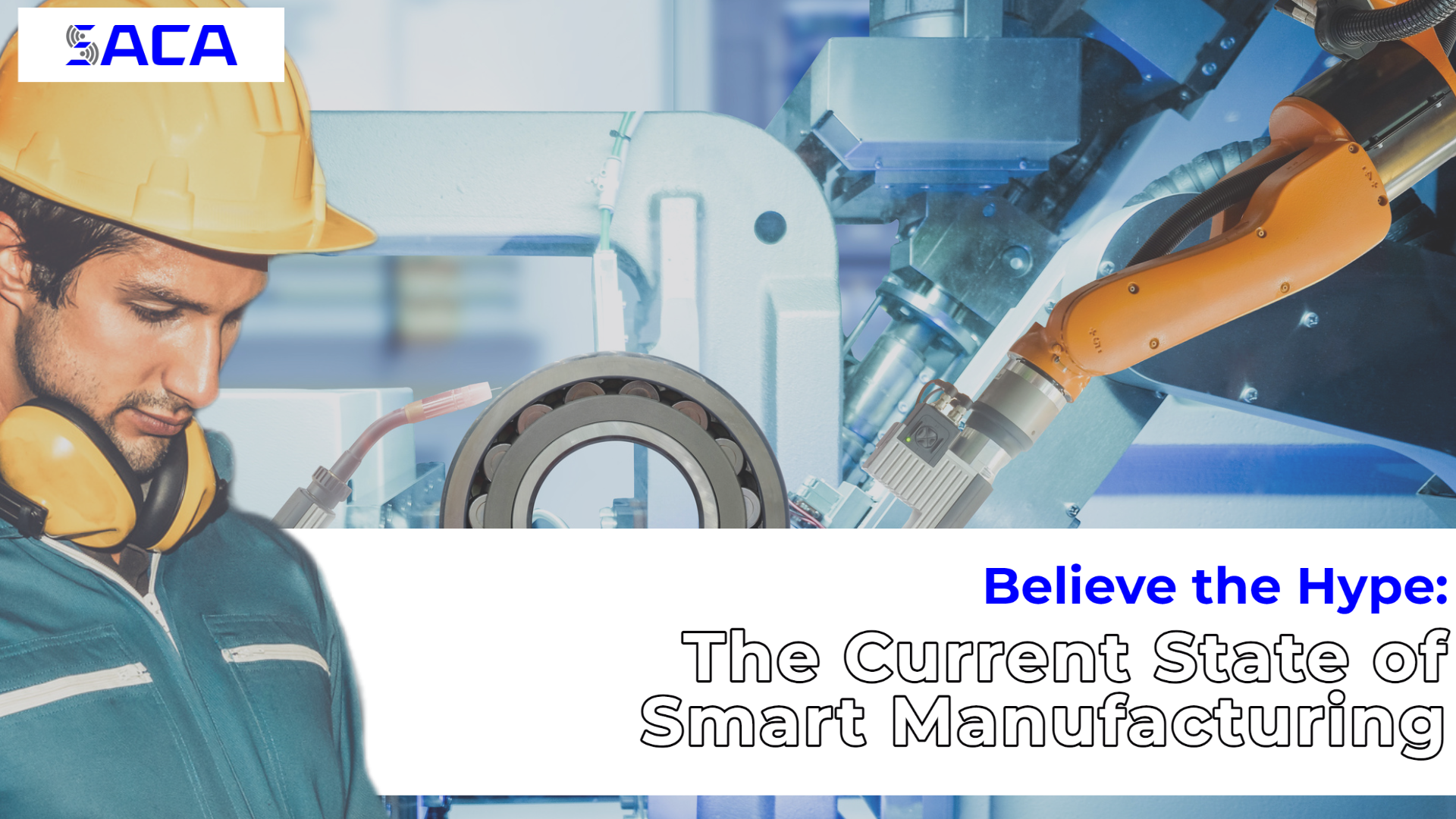
It’s no secret that technology has changed our personal lives in ways few could have foreseen decades ago. But to what extent has technology changed the way we work?
People unfamiliar with the manufacturing sector might assume that factories where people work with their hands to make things might not be on the frontier of technological progress. However, they might be surprised to learn that the nation’s manufacturing facilities are driving forces when it comes to advanced technology.
There’s even a name for the technological revolution taking place throughout manufacturing: Industry 4.0. This term refers to the fact that we’re in the midst of a fourth Industrial Revolution, in which advanced automation technologies powered by Internet-connected systems are transforming the way modern manufacturing facilities operate.
This phenomenon goes by a variety of different monikers, including Smart Factory, the Industrial Internet of Things (IIoT), and Smart Manufacturing. It’s gotten a lot of attention over the past several years, leading some to question whether all the hype is justified.
After all, there are plenty of people who work in facilities that remain largely unchanged from the way they’ve always been. Is technology really transforming manufacturing the way the media portrays?
In a nutshell, the answer is yes. If you haven’t jumped aboard the Industry 4.0 train yet, it’s time to make your way to the station. Believe the hype. The current state of manufacturing is smarter and more automated than ever before, and it’s only growing and accelerating. As Blake Moret, Chairman and Chief Executive Officer of Rockwell Automation, recently noted, “We’ve experienced 20 years of evolution in 2 years.”
In this article, we’ll take a closer look at a few of the conclusions reached by experts at Rockwell Automation and Plex, in association with Sapio Research, in their Eighth Annual State of Smart Manufacturing Report (the “report”).
Challenges Spurring Technology Investments
Why are so many manufacturers choosing to invest in advanced smart automation technologies? That’s one of the questions the authors of the report looked at when developing questions for their survey of 1,353 global manufacturers across 13 of the top manufacturing countries.
What they learned is that many manufacturers see technology as a means to address one or more of the many challenges they face in today’s manufacturing environment. For example, “[s]killed labor – and labor of any kind – continues to be elusive across the globe. As manufacturers continue to seek opportunities for profitable growth, they’re finding that uncertainty in workforce availability is impacting quality, along with their ability to meet their customers’ needs and transform at pace. They are addressing this impact by using technology to extract data from their operations and assemble actionable insights.”
As manufacturers compete for skilled labor, they’re also competing with other manufacturers globally for customers and market share. The authors of the report “are also seeing how technology is helping the industry accelerate their agility and competitive differentiation.”
In fact, “manufacturers view technology as an advantage for improving quality, agility, innovation, and to attract the next generation of talent. Manufacturers expect to mitigate risk through technology tied to processes and people to build resiliency and drive future success.”
The Current State of Smart Manufacturing
Knowing that manufacturers are increasingly turning to advanced automation technologies to address the many challenges they’re facing, the authors of the report sought to gauge both the current levels of technology adoption and manufacturers’ plans for the future.
Before jumping into those findings, though, it’s important to understand what we’re talking about when we refer to “smart manufacturing.” According to the Manufacturing Enterprise Solutions Association (“MESA International”), “Smart Manufacturing is the intelligent, real-time orchestration and optimization of business, physical, and digital processes within factories and across the entire value chain. Resources and processes are automated, integrated, monitored, and continuously evaluated based on all available information as close to real time as possible.”
Manufacturers embracing smart manufacturing technologies are doing so “to mitigate risks, open up new opportunities, and remain competitive.” In terms of risk management, manufacturers face both internal and external risks.
According to the report, “[t]he top two ways respondents are addressing internal risk are to adopt new technology aimed at minimizing disruption from workforce or supply issues (53%) and to shift their operations to the cloud for purposes including increased cybersecurity protection and business continuity (50%). When it comes to external risks like inflation, supply chain, and workforce shortages, the top-ranking mitigation tactic is adopting new technology (44%).”
So exactly how many respondents are we talking about? The report concludes that “[e]ighty-four percent of respondents have adopted smart manufacturing or are actively evaluating solutions with the intention to invest in the coming year.” That’s an astounding adoption rate, which shows clearly the role these technologies play today and will continue to play in the future.
The report did note a difference in adoption rate based upon available revenue: “Companies with higher revenues are more likely to have adopted smart manufacturing technology, with a 58% adoption rate among respondents in the top third for revenue, compared to 40% among the lower revenue bracket.”
This finding is unsurprising, but the report indicates it “may indicate an opportunity for small and mid-size organizations to leverage an incremental, lower initial cost and resource approach to smart manufacturing with modular solutions that provide strong value and quick time to payback and ROI.”
With manufacturing becoming a more global phenomenon every year, it’s worth noting that investment in advanced automation technologies isn’t limited to the United States. Indeed, the top three countries with the greatest adoption rates of smart manufacturing technologies are “China (70%), the US (60%) and India (57%).”

Smart Manufacturing Solutions Abound
So what exactly are these advanced automation technologies we’re talking about when we discuss smart manufacturing? The report summarizes a set of ten smart manufacturing solutions manufacturers are adopting:
- Smart Devices
“Smart devices are self and system-aware assets that acquire and process operating data – and monitor and report on asset conditions such as self-diagnostics and energy usage.”
- Manufacturing Execution Systems (MES)
“Manufacturing Execution Systems (MES) track and document the transformation of raw materials into finished goods, providing real-time production management to drive enterprise-wide compliance, quality, and efficiency.”
- Quality Management Systems (QMS)
“Quality Management Systems (QMS) standardize and automate quality documentation, processes, and measurements.”
- Computerized Maintenance Management Systems (CMMS)
“Computerized Maintenance Management Systems (CMMS) help organizations track and manage maintenance and repair activities for their facilities, equipment, and other assets in one place.”
- Asset Performance Management (APM)
“Asset Performance Management (APM) combines process, operational, and machine-level data through dashboards to monitor machine and plant health, ensuring optimal uptime, throughput, and maintenance needs.”
- Production Monitoring
“Production Monitoring provides seamless connectivity to machines on the plant floor, delivering transparent, real-time operational KPIs like OEE and dashboards to drive continuous improvements.”
- Distributed Control Systems (DCS)
“Distributed Control Systems (DCS) use decentralized elements to control dispersed systems, such as automated industrial processes or large-scale infrastructure systems.”
- Supply Chain Planning (SCP)
“Supply Chain Planning (SCP) combines data from multiple departments across the business or from outside market resources to sync demand and supply forecasting to improve inventory accuracy and production management.”
- Enterprise Resource Planning (ERP)
“Enterprise Resource Planning (ERP) automates front- and back-office processes, including financial management, revenue management, human capital, order management, billing, and inventory.”
- Analytics
“Analytics use data to solve manufacturing bottlenecks, optimize output and quality, and provide new insights.”
Contact SACA to Learn More about Smart Automation Certifications
As manufacturers incorporate these new advanced automation technologies, they’re finding they need workers with more advanced technical and technological skills than ever before. Unfortunately, there aren’t enough workers with these skills to fill the many roles available today, creating what is known throughout industry as the “skills gap.”
How can manufacturers find the highly-skilled workers they need so desperately? One promising solution is the development of industry-standard certifications that focus on connected-systems skills. The Smart Automation Certification Alliance (SACA) sits at the forefront of the effort to certify students and workers who demonstrate the required knowledge and hands-on smart automation skills employers so desperately need.
To learn more about Industry 4.0 certifications and how SACA can help both educational institutions and industry employers begin the task of bridging the Industry 4.0 skills gap, contact SACA for more information.
About Duane Bolin
Duane Bolin is a former curriculum developer and education specialist. He is currently a Marketing Content Developer for Amatrol, Inc. Learn more about Amatrol and its technical training solutions, including eLearning, here and connect with Duane on Amatrol’s Twitter, Facebook, LinkedIn, and YouTube pages.