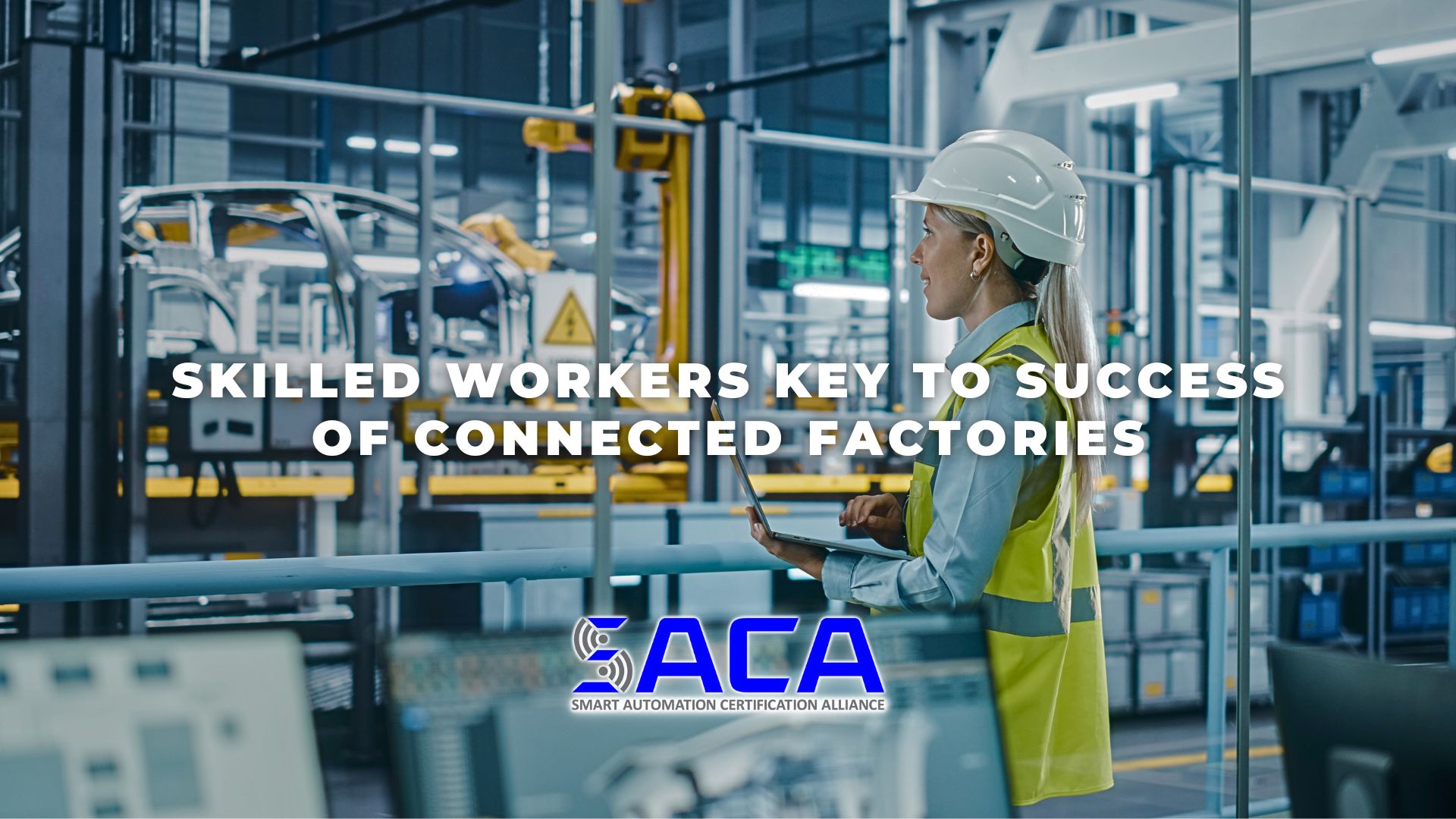
In recent weeks, manufacturing has once again been a popular topic of conversation amidst the Trump administration’s on-again/off-again tariff announcements. Proponents of tariffs believe they will force companies to reshore manufacturing that has been previously moved overseas.
However, people familiar with the current state of manufacturing in the United States know things aren’t nearly as simple as they’re made to seem on the news. Already facing an ongoing skills gap that has left more than a half-million manufacturing jobs unfilled, where will manufacturers find even more workers to fill new factories?
Many Americans do agree that it would be a good thing if there were more manufacturing workers in the U.S. However, far fewer people think manufacturing would be a good fit for themselves personally. This lasting negative impression of manufacturing as a career choice is one of the primary contributing factors to the ongoing skills gap plaguing manufacturers across the country.
Over the past couple of decades, American manufacturers have attempted to deal with the skills gap in a variety of ways. For example, many manufacturers have invested heavily in advanced automation technologies that can increase productivity and efficiency while reducing the need for human workers in certain types of jobs. These facilities feature “connected systems” technologies that create what many refer to as a “smart factory” environment.
This use of robots and other automation technologies has led some to worry that human workers would be completely displaced by technology one day. To the contrary, though, many of these technologies are merely taking the place of workers that couldn’t be found in the first place. For those who worry about robots replacing humans, new research should give them comfort that human beings in the workplace will always be necessary…and even more so in the age of advanced automation.
A DC Velocity article summarizes recent research by Gartner, which found that a “human-centric strategy is key to operating the ‘connected factory.’” “According to Gartner, connected factory workers use digital tools and data management techniques to improve how work is done in factories. That access to new knowledge and technology reduces variability, decentralizes decisions, and proliferates knowledge.”
Although the focus is often on the technology being implemented, Gartner “emphasizes the role of the connected factory worker in the advancement of an overall smart manufacturing strategy…The connected factory worker can serve as a strategic pillar in supporting an organization’s aim of localizing manufacturing and expanding capacity.”
As manufacturers navigate the complex pathway of combining advanced automation technologies with highly skilled workers who can install, operate, maintain, troubleshoot, and repair these systems, finding the right type of workers who can thrive alongside technology will be paramount.
“Successful implementation of these initiatives is key to overcoming labor shortages, revitalizing the frontline workforce and reinventing the employee value proposition in manufacturing for a new generation.”
Involving workers in the decision-making process early can be beneficial. “In the near-term, they can achieve operational cost savings, while in the longer-term they may gain strategic benefits centered on enhancing the employee experience, upskilling talent, and creating new organizational roles that will appeal to and engage the next generation of workers.”
So where do these connected factory workers come from? As companies embrace new technologies, they will often need to either upskill current workers or hire new workers with the advanced automation technology skills they require.
If hiring new workers ends up being part of their automation implementation plan, manufacturers should look for candidates with industry-standard credentials that prove they already possess the advanced automation skills needed to thrive.
For example, if workers possess a certification from the Smart Automation Certification Alliance (SACA), employers can feel confident they’ve already proven they have the knowledge and hands-on skills needed for working with advanced smart automation technologies. SACA has been hard at work collaborating with industry leaders to develop a wide variety of industry-standard certifications that will help employers find workers who possess the advanced connected-systems skills they need to take their businesses to the next level. Be sure to check out SACA and all it has to offer!