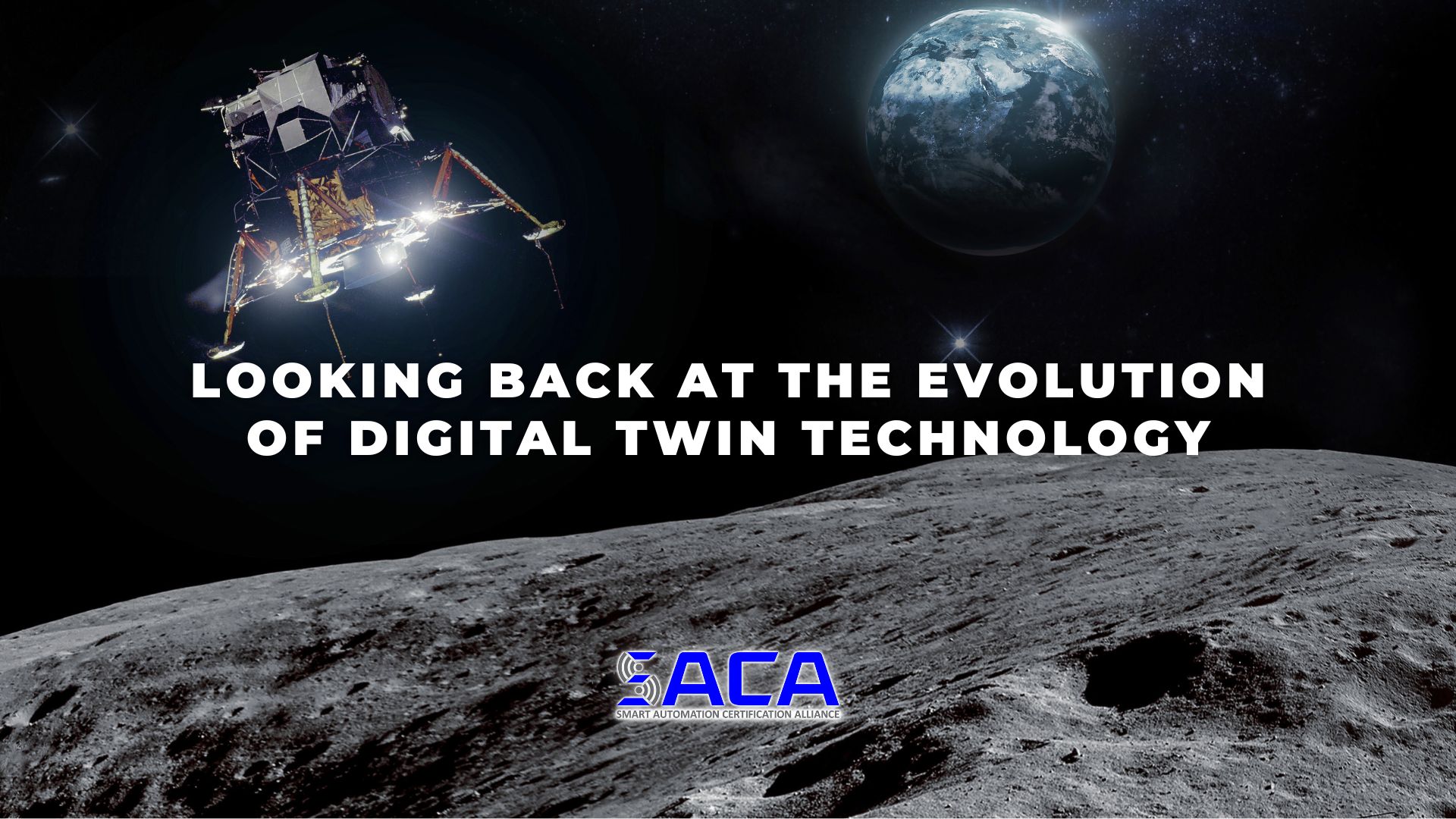
Would you believe that one of the most modern technologies currently transforming manufacturing can be traced back decades to our attempt to reach the Moon? That may surprise many people who understand that we reached the Moon with technology most would consider primitive compared to what we take for granted today.
NASA’s Apollo program landed men on the Moon before there was an Internet using computers that weighed 140 pounds and boasted 64kb of memory, not even enough to store the amount of text in the average book. The feats pulled off by the Apollo program were mind-blowing, and the legacy of the program was a wide variety of advancements, like the integrated circuit, fireproof materials, and freeze-dried food.
In a recent Forbes article, author Raghunandan Gurumurthy points out another significant modern technology that can give thanks to the Apollo program: digital twins. According to Gurumurthy, “[t]he concept of digital twins traces back to NASA’s Apollo program, where engineers created detailed simulators to troubleshoot spacecraft systems from Earth.”
The author notes that “it was only with the dawn of the Internet of Things (IoT) and big data analytics that digital twins found their true calling in manufacturing.” He believes manufacturers will soon embrace their power: “Imagine a world where every product, machine and process has a virtual counterpart—a dynamic, data-driven replica that lives in the cloud.”
Gurumurthy believes digital twins have a “unique ability to provide unprecedented insights and control over the manufacturing process.” For example, he has personally used digital twin technology “to optimize assembly line efficiency, significantly reducing energy consumption and material waste.”
Digital twins hold great potential in a variety of manufacturing applications. For example, “[i]n warehouse operations, digital twins can prove invaluable for redesigning layouts, maximizing space utilization through dynamic storage and improving product flow.”
According to Gurumurthy, the real-time monitoring abilities of digital twins can revolutionize maintenance, too: “By continuously analyzing data from sensors embedded in machinery, digital twins can predict when equipment will likely fail. This predictive maintenance approach can decrease downtime and extend the lifespan of manufacturing equipment, reducing waste and the need for replacements.”
As occurs whenever any new advanced automation technology finds a foothold in manufacturing, some people are concerned that digital twins will cause job displacement. Gurumurthy believes that “the reality is more likely a shift in skills.” Rather than replacing workers, digital twins will require workers with advanced automation skills to work alongside them.
It’s important to ensure skilled personnel are available to operate, maintain, troubleshoot, and repair these new technologies as implemented. In many cases, that will mean either upskilling current workers or hiring new workers with the advanced automation technology skills you require.
If hiring new workers ends up being part of your automation implementation plan, look for candidates with industry-standard credentials that prove they already possess the advanced automation skills needed to thrive. For example, if workers possess a certification from the Smart Automation Certification Alliance (SACA), employers can feel confident they’ve already proven they have the knowledge and hands-on skills needed for working with advanced smart automation technologies. SACA has been hard at work collaborating with industry leaders to develop a wide variety of industry-standard certifications that will help employers find workers who possess the advanced connected-systems skills they need to take their businesses to the next level. Be sure to check out SACA and all it has to offer!