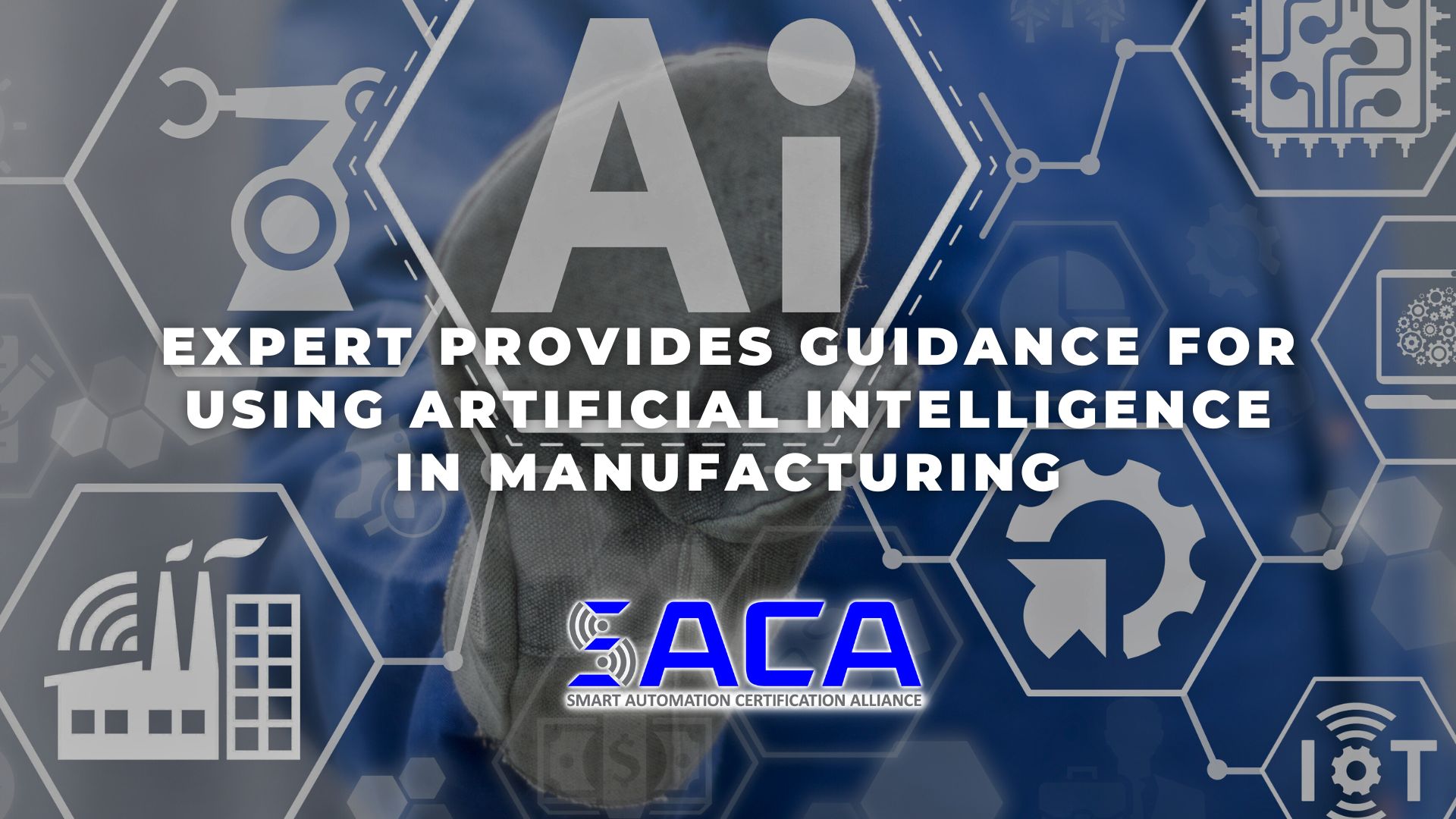
Unless you’ve been living under a rock over the course of the past year, then you’ve definitely heard of—and possibly even used—generative artificial intelligence (AI), such as ChatGPT. AI has really taken off over the past year or more, and it’s easy to see how useful it can be in areas like software programming and marketing.
But what about manufacturing? With an ongoing skills gap making the manufacturing labor market especially tight, manufacturers are searching for any way to increase productivity and efficiency. Could AI be a solution to their problems?
Those familiar with manufacturing already know that change usually happens incrementally. That’s a polite word for slowly, by the way. AI, however, is a technology associated with exponential, rapid change. Does such technology have a place in the world of manufacturing?
In a recent Chief Executive article, author Dan Bigman details his conversations with Pavan Muzumdar, chief operating officer of Automation Alley, Michigan’s Industry 4.0 knowledge center. According to Muzumdar, generative AI, like ChatGPT, can have a positive impact in manufacturing, if it’s implemented in the right way for the right reasons.
For example, Muzumdar recommends manufacturers “use gen AI to get started on something, use gen AI for ideation, use gen AI to kind of get you a little bit further ahead. But don’t use gen AI for completion.”
Muzumdar also advises that manufacturers “[b]e very cautious in using gen AI for factual information…whatever you ask AI to do, ask it so that the output that you get is in a chunk that you can independently verify. You can get great value, but make sure that you’re doing this ‘trust but verify’ type of approach.”
One successful application many manufacturers have found for AI is helping with old technologies. Many new manufacturing hires don’t know older programming languages, like COBOL, that might still be used in legacy systems. Generative AI can help new programmers decipher old code and write new code in languages they’re not familiar with.
Likewise, generative AI can help a new worker who understands general programming but not, for example, something specific to manufacturing, like CNC programming. According to Muzumdar, these workers “can kind of inductively learn how to do CNC programming just with the help of gen AI. But again, don’t trust it fully; learn how to use it and then verify that by making sure that you’re actually doing some physical tests to see that it’s actually giving you the results.”
Bigman believes that manufacturers should remember that “a gen AI like ChatGPT has digested almost every user’s manual and how-to guide, best practice guide on almost every machine that’s sitting on your shop floor.” Even if it can’t solve every one of your problems, it can accelerate understanding and speed along the process.
Muzumdar agrees, reminding that “[i]t’s not AI, it’s human plus AI. How can I empower my own staff to be much more open about it, knowing that it has limitations, but even things with limitations can have substantial value in making us much more productive.”
Even if AI does not replace workers, the workers of today and tomorrow will need to learn new skills to keep pace with the advanced technologies being implemented in the modern workplace. That’s why manufacturers are increasingly looking to hire highly skilled workers that can operate, maintain, troubleshoot, and repair advanced automation systems.
Unfortunately, due to the ongoing “skills gap” facing industries across the country, finding highly skilled workers remains a significant challenge. How can employers be sure that workers have the hands-on skills they need to succeed in the modern workplace? Today, more and more employers are looking for workers with industry-standard certifications that prove they have the skills needed.
For example, if workers possess a certification from the Smart Automation Certification Alliance (SACA), employers can feel confident they’ve already proven they have the knowledge and hands-on skills needed for working with advanced smart automation technologies. SACA has been hard at work collaborating with industry leaders to develop a wide variety of industry-standard certifications that will help employers find workers who possess the advanced connected-systems skills they need to take their businesses to the next level. Be sure to check out SACA and all it has to offer!