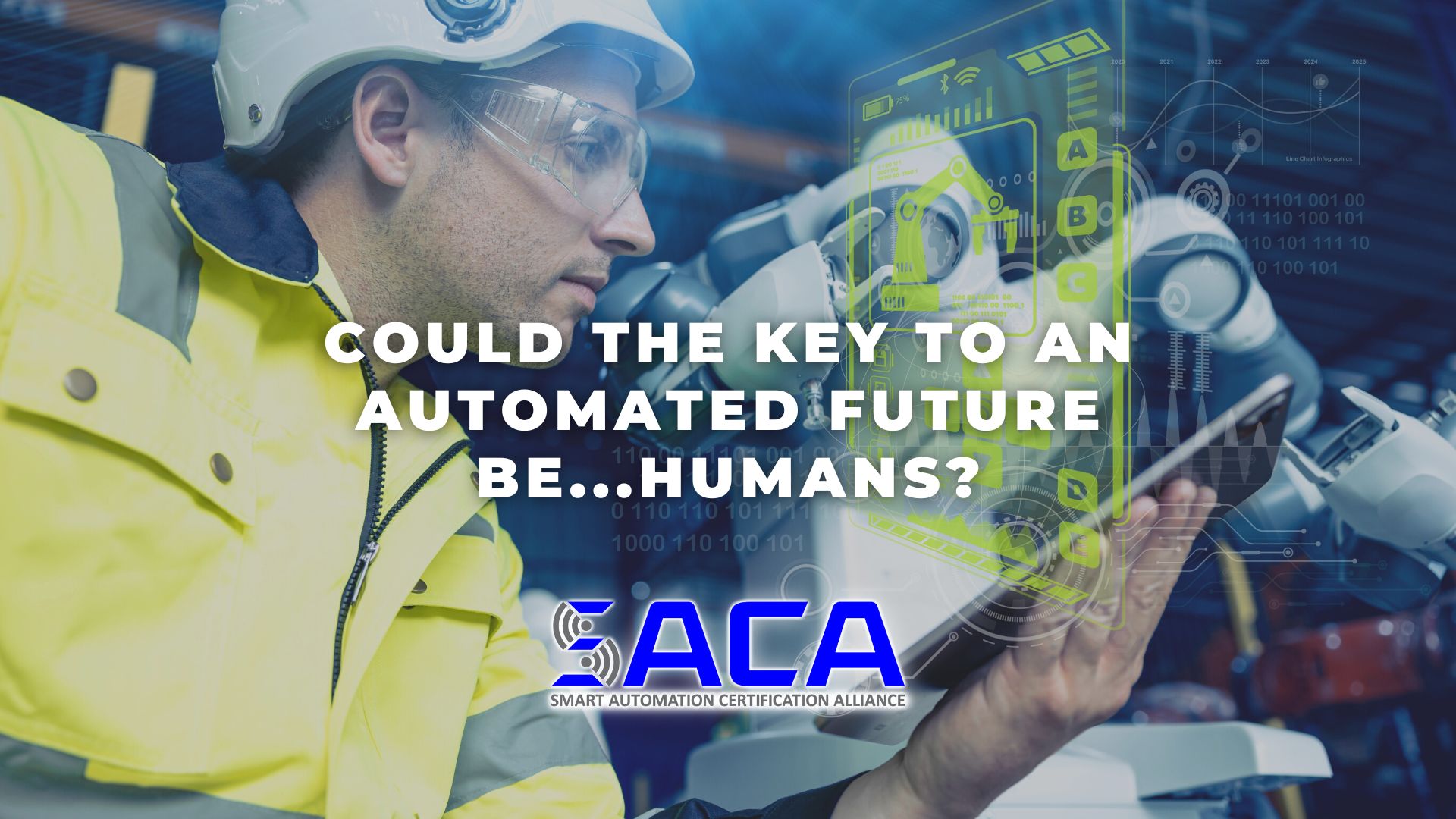
“The robots will steal all our jobs!” That’s the familiar refrain you’ve probably heard time and again when industries implement advanced automation technologies, such as robots, automated guided vehicles, machine learning, and artificial intelligence.
But is there any truth to it? While advanced automation technologies may indeed replace human workers in areas where tasks are dangerous and/or repetitive, industry experts focus instead on the new roles created when new technologies enter the workplace.
Automation experts have always known that advanced automation technologies wouldn’t completely replace human workers. However, it’s becoming clear in factories everywhere that the secret ingredient to ensuring that these advanced technologies operate efficiently and productively is…ironically…human beings.
Specifically, the human beings modern automated workplaces need are so-called “connected workers.” According to a recent Automation World article by Eric Whitley, “[c]onnected workers are the human component within a sophisticated network of automated machinery, ensuring that systems run smoothly and efficiently. They provide the insight and oversight that machines alone cannot, adjusting operations in real-time based on data-driven feedback.”
Highly skilled, connected workers are “equipped with digital tools to interact with and control automated systems. Their key responsibilities include monitoring system performance, managing workflow adjustments and providing on-the-spot problem-solving.”
Companies that have already implemented a connected worker model report “significant improvements in operational efficiency and product quality…[via] fewer errors, reduced downtime and a more engaged workforce…transform[ing] traditional manufacturing environments into dynamic, responsive systems.” Connected worker success stories can be found at places like Siemens, General Motors, and Boeing.
So, what kinds of workers make the best connected workers? According to Whitley, “[c]onnected workers must possess a blend of traditional manufacturing skills and digital literacy. They need to understand not only the mechanics of the machinery but also how to analyze and interpret data. Equally important is their ability to interact with advanced technological interfaces that are central to modern automated systems.”
Connected workers “must be willing to update their skills regularly to keep pace with technological advances.” Likewise, companies seeking to automate must be willing to invest in ongoing training. “Companies that foster a culture of lifelong learning are better positioned to capitalize on the benefits of factory automation.”
Whitley notes that “[t]o prepare workers for these evolving roles, training methodologies have become more innovative, often employing virtual reality and simulation-based learning. These tools offer hands-on experience in a controlled environment, enabling workers to master complex systems without the risks associated with live operations.”
What steps does your organization need to take to effectively implement a connected worker model at your facility? In addition to upskilling current workers, employers need to ensure that new workers have the hands-on skills they need to succeed.
Today, more and more employers are looking for workers with industry-standard certifications that prove they have the skills needed. For example, if workers possess a certification from the Smart Automation Certification Alliance (SACA), employers can feel confident they’ve already proven they have the knowledge and hands-on skills needed for working with advanced smart automation technologies. SACA has been hard at work collaborating with industry leaders to develop a wide variety of industry-standard certifications that will help employers find workers who possess the advanced connected-systems skills they need to take their businesses to the next level. Be sure to check out SACA and all it has to offer!